
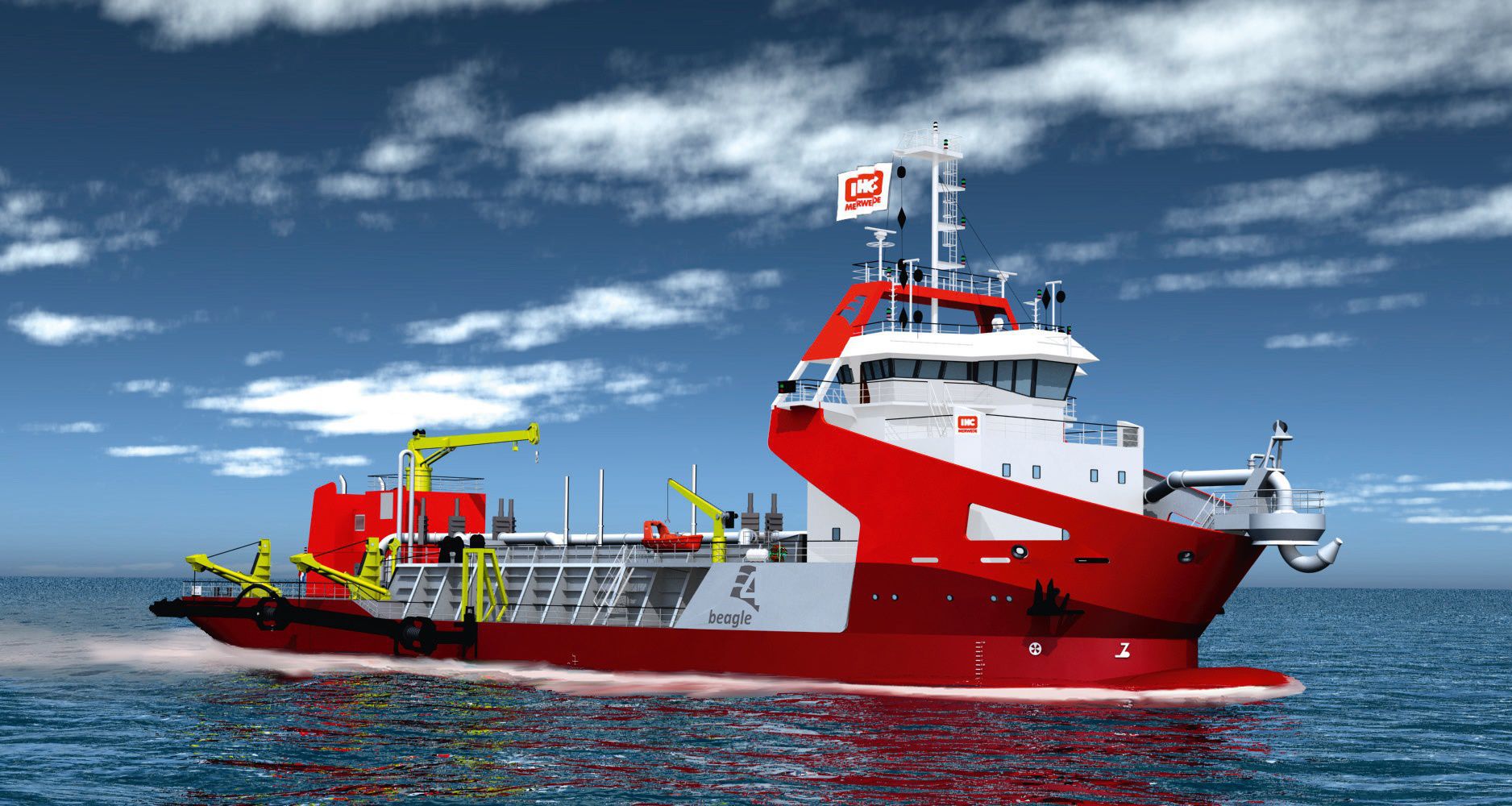
In such cases, other types of dredges may be more suitable for removing the contaminated sediments from the channel prism. When contaminated sediments are to be dredged and adverse environmental effects have been identified, pumping past overflow is not recommended. If the material being dredged is clean sand, the percentage of solids in the overflow will be small and economic loading may be achieved by pumping past overflow. The environmental effects of these methods must be assessed on a project-by-project basis. Legislation and the water quality certification permits required by the various states in which dredging is being accomplished. The use of these methods is controlled to varying degrees by environmental Hopper dredging is accomplished by three methods: (a) pumping past overflow, (b) agitation dredging, and (c) pumping to overflow. Before there were environmental restrictions, hopper dredges were operated with the primary objective of obtaining the maximum economic load i.e., removing the maximum quantity of material from the channel prism in the shortest pumping time during a day's operation. Because of the limitations on open-water disposal, most hopper dredges have direct pumpout capability for disposal in upland confined Unloading is accomplished either by opening doors in the bottoms of the hoppers and allowing the dredged material to sink to the open-water disposal site or by pumping the dredged material to upland disposal sites. Once fully loaded, hopper dredges move to the disposal site to unload before resuming dredging. The dredged material is sucked up the pipe and deposited and stored in the hoppers of the vessel.

The drag is moved along the channel bottom as the vessel moves forward at speeds up to 3 mph. Suction pipes (dragarms) are hinged on each side of the vessel with the intake (drag) extending downward toward the stern of the vessel. Hopper dredges are equipped with large centrifugal pumps similar to those employed by other hydraulic dredges. Dredging is accomplished by progressive traverses over the area to be dredged. Operation of a seagoing hopper dredge involves greater effort than that required for an ordinary ocean cargo vessel, because not only the needs of navigation of a self-propelled vessel but also the needs associated with its dredging purposes must be satisfied. They are equipped with twin propellers and twin rudders to provide the required maneuverability. During dredging operations, hopper dredges travel at a ground speed of from 2 to 3 mph and can dredge in depths from about 10 to over 80 ft. Hopper dredges are classified according to hopper capacity: large-class dredges have hopper capacities of 6000 cu yd or greater, medium-class hopper dredges have hopper capacities of 2000 to 6000 cu yd, and small-class hopper dredges have hopper capacities of from less than 2000 to 500 cu yd. Dredged material is raised by dredge pumps through dragarms connected to drags in contact with the channel bottom and discharged into hoppers built in the Hopper dredges have propulsion power adequate for required free-running speed and dredging against strong currents and excellent maneuverabilityįor safe and effective work in rough, open seas.
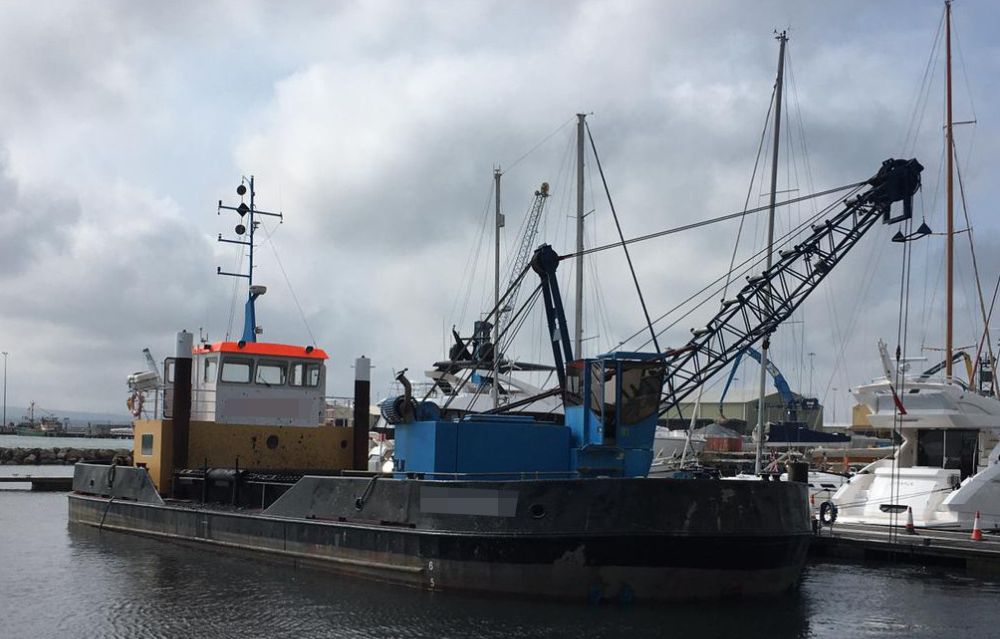
They are equipped with propulsion machinery, sediment containers (hoppers), dredge pumps, and other special equipment required to perform their essential function of removing material from a channel bottom or ocean bed. Hopper dredges are self-propelled seagoing ships of from 180 to 550 ft in length, with the molded hulls and lines of ocean vessels.
